Master Cylinders
Brake fluid movement and pressure are created by the master cylinder. The difference in piston size means that by the time the braking force reaches the calipers it has been increased to about 26 times your initial input at the lever…
Single Master Cylinder
The simplest master cylinder have a single piston to operate both front discs or the single rear disc on a motorcycle. In cars they have been replaced by a tandem master cylinder in which there are two pistons - one operating front right hand and rear left hand brakes and the other operating the front left and rear right hand brake so that in the event of failure two opposite brakes still work.
Obviously this isn't able to be replicated on a motorcycle braking system with only two discs instead of four but AP Lockheed have copied the idea to manufacture a twin master cylinder. One piston operates the right hand disc and the other the left hand disc which is a good safety device in that with the failure of one caliper or hose the other can still operate meaning some braking ability is retained in the system.
Most hydraulic fluid reservoirs are integral with the master cylinders and are directly above the piston but some have a remote reservoir connected to the master cylinder via a small hose (Brembo for example). the piston is moved forward in the cylinder via the brake lever. The piston is returned by a spring against the piston when lever force is removed. There are two holes, called ports, in the master cylinder which allow fluid to enter the cylinder. These are called the fluid inlet port and the compensating port. When the piston is at rest the compensating port is just ahead and the fluid inlet port is just behind the lip forming the front face of the piston. In this position the piston rests against a clip or retaining ring that prevents the spring return from pushing the piston out of the end of the cylinder.
As the brakes are applied the piston moves forward with the lip of the seal covering the compensating port. Before this port is covered, piston motion forces excess fluid back into the reservoir. If you look into a reservoir just as the piston begins to move you will see slight fluid motion. Once the compensating port is covered, fluid trapped in the hydraulic system cannot escape provided there are no leaks in the system. Beyond this position the piston moves fluid to apply the brakes.
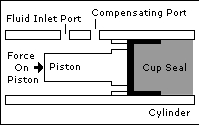
Initial fluid movement reduces clearances in the system. When all clearances are eliminated the fluid stops moving and pressure rises to the maximum you and the system can obtain. When the lever is released hydraulic pressure is reduced, the disc pistons retract and the master cylinder piston moves back to the retaining pin due to the spring return operating.
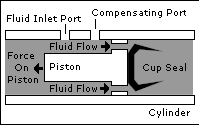
The fluid inlet port function is more complicated. The piston has small holes drilled into it through the front face lip. the cup seal is installed ahead of this face with the lip extending forward. the fluid inlet port allows fluid behind the front lip of the piston, the holes allowing fluid to contact the seal face. this helps with brake release when the piston returns. As the brakes are released the return spring may move the piston faster than the fluid can move. When this occurs the seal lip is drawn away from the cylinder wall allowing fluid to flow through the small holes in the seal lip. This keeps fluid ahead of the piston at all times and prevents the formation of tiny bubbles in front of the piston which would cause a spongey brake with excessive travel. The secondary seal stops any fluid leaking out of the open end of the cylinder.